Injection Mold in the process of processing makes everyone annoyed is some common defects; these defects will directly lead to the performance of the workpiece, and even lead to the workpiece can not be used in this, so we are in the mold processing, must try to avoid some defects, the following seven methods for this problem.
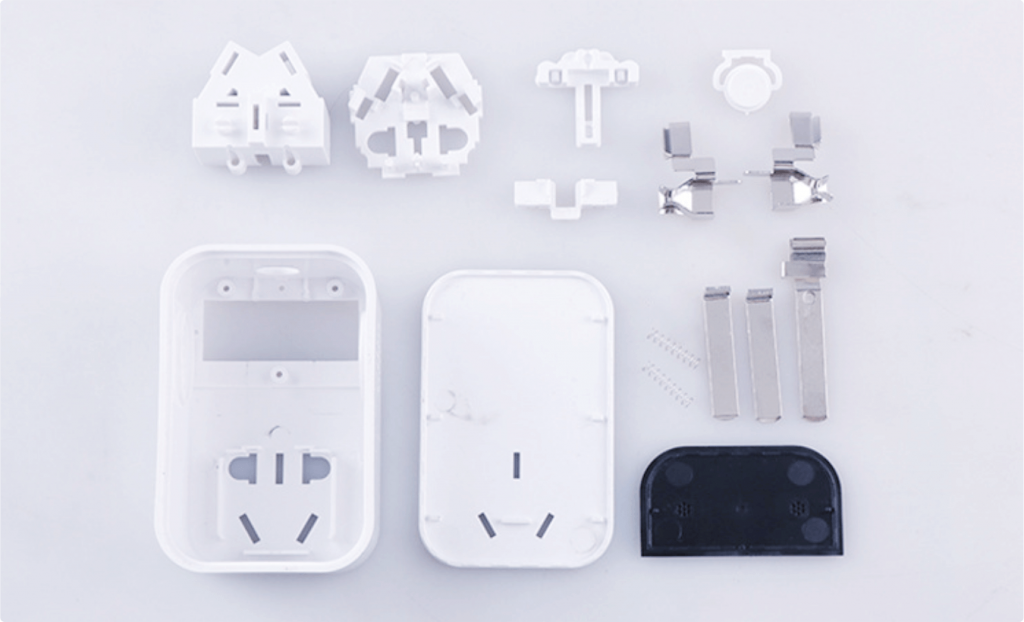
1. The reasonable choice and dressing grinding wheel, using white corundum grinding wheel is better, it is the performance of hard and brittle, and easy to produce the new cutting edge, so the cutting force is small, the grinding heat is small, use medium granularity on granularity, such as 46 ~ 60 mesh is better, on the grinding wheel hardness by using soft and soft (ZR1, ZR2, and R1, R2). Namely, coarse granularity, low hardness of the grinding wheel, Good self-excitation can reduce cutting heat.
Selecting the appropriate fine grinding wheel is very important. Because of the die steel condition with high vanadium high molybdenum, choosing GD is suitable for single crystal corundum grinding wheel. When processing hard alloy, high quenching hardness of materials, the priority of using an organic binder of diamond grinding wheel, since the organic binder grinding wheel grinding, grinding the workpiece roughness of Ra0.2 mum, in recent years, With the application of new materials, CBN (cubic boron nitride) grinding wheel shows excellent processing effect.
It is superior to other grinding wheels in finishing machining on CNC forming grinders, coordinate grinders, and CNC internal and external grinding machines. In the grinding process, attention should be paid to timely dressing the grinding wheel to keep the grinding wheel sharp. When the grinding wheel is passivated, it will slip and rub on the surface of the workpiece, resulting in surface burns and reduced strength.
2. Mold processing reasonable use of cooling lubrication fluid, cooling, washing, lubrication of the three roles, keep the cooling lubrication clean, control the grinding heat within the allowable range, and prevent thermal deformation of the workpiece. Improve the cooling conditions during grinding, such as using the oil-sand wheel or internal cooling grinding wheel and other measures. By introducing the cutting fluid into the center of the grinding wheel, the cutting fluid can directly enter the grinding zone to play an effective cooling role and prevent the workpiece surface from being burned.
3. The quenching stress after heat treatment is reduced to the minimum because the quenching stress, network carbonization structure under the action of grinding force, the structure of phase transformation is easy to crack the workpiece. In order to eliminate the residual stress of grinding for precision die, low-temperature aging treatment should be carried out after grinding to improve toughness.
4. Laminate grinding stress can also be the mold in 260~315℃ salt bath soak 1.5min, and then cool in 30℃ oil so that 1HRC can reduce the hardness, residual stress reduced by 40%~65%.
- 5. For precision grinding of precision die with size tolerance within 0.01mm, attention should be paid to the influence of ambient temperature, and constant temperature grinding is required. According to the calculation, when the temperature difference is 3℃, the material changes about 10.8μm (10.8=1.2×3×3, the deformation per 100mm is 1.2μm/℃), and the influence of this factor should be fully considered in all finishing processes.
6. Using electrolytic grinding processing improve mold manufacturing accuracy and surface quality. In electrolytic grinding, the grinding wheel scrapes the oxide film instead of grinding the metal, so the grinding force is small, the grinding heat is small, no grinding burrs, cracks, burns, and other phenomena, the general surface roughness can be better than Ra0.16μm.
In addition, the wear of the grinding wheel is minor; in hard alloy grinding, the wear of the silicon carbide grinding wheel is about 400%~600% of the weight of hard alloy grinding off; when grinding with electrolysis, the wear of the grinding wheel is only 50%~100% of the hard alloy grinding.
7. Reasonable selection of grinding amount, small radial feed grinding method, or even fine grinding. Suppose the radial feed and grinding wheel speed are adequately reduced, increasing the axial feed. In that case, the contact area between the grinding wheel and workpiece is reduced, and the heat dissipation condition is improved to control the increase of surface temperature effectively.
Try Made by Aria Now
All information and uploads are secure and confidential.
Categories
Share On
Recent Post
What is Overmolding? A Complete Guide
In today’s manufacturing world, creating durable, functional, and aesthetically pleasing
A Complete Guide on the Types Of Screw Head
You’ve probably stood in front of a confusing display of