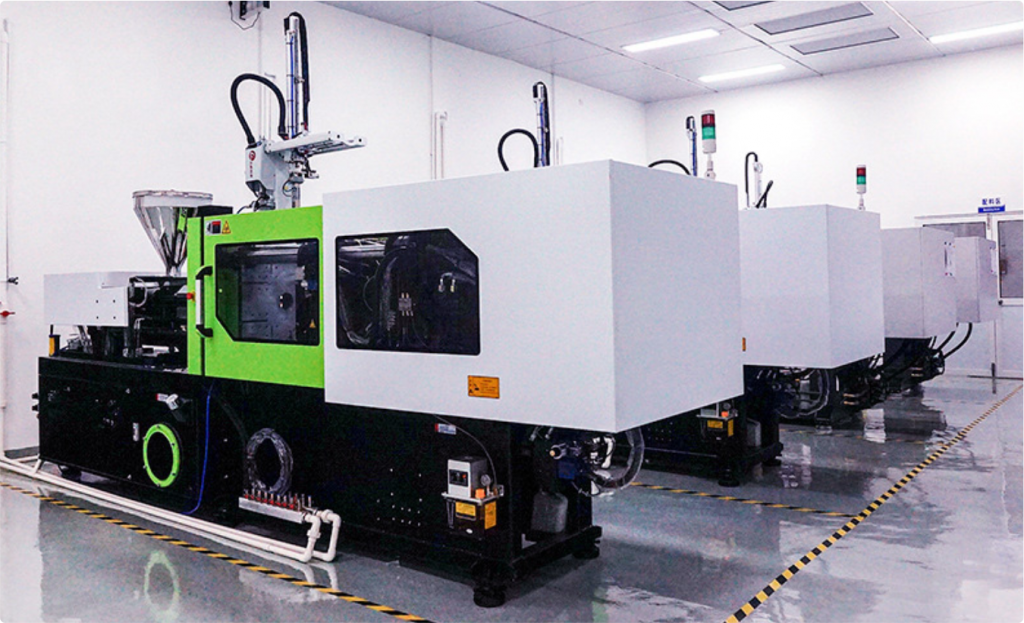
What is plastic injection molding, Types of Molding and Industries that use it already?
What is plastic injection molding, Types of Molding and Industries that use it already?
Plastic is one of the most widely used materials for many industries today. This is because it’s easy to mold into many shapes, it can be made to look like metal, wood, or other materials, and it’s durable. One of the biggest problems with plastic, however, is that it tends to crack or break over time. To solve this problem, manufacturers use plastic injection molding. This is how it works.
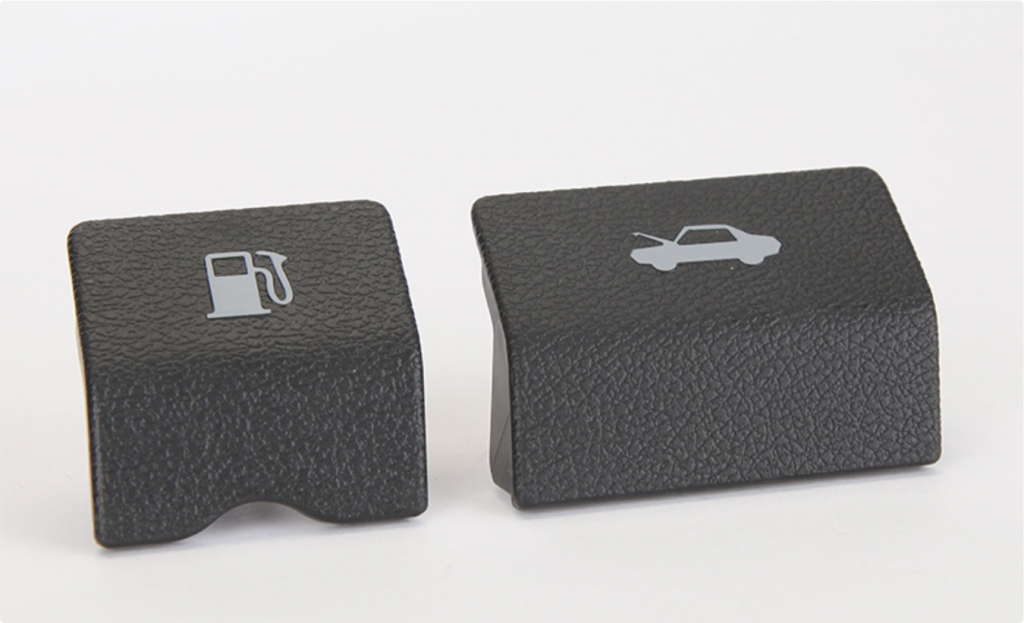
1. What is plastic injection molding?
Plastic injection molding is a manufacturing process for producing parts from both thermoplastic and thermoset polymers. Injection molding is popular because it can create complex shapes that are difficult or impossible to make with other manufacturing methods. It also has a high production rate and can create parts with a wide range of sizes.
2. How does plastic injection molding work?
Plastic injection molding is a process by which a thermoplastic material is melted and injected into a mold. The mold is then cooled and the resulting part is ejected. The process is repeated until the desired number of parts are produced.
3. Types of plastic injection molding
(Acrylonitrile Butadiene Styrene) ABS Injection molding material
ABS is a type of plastic that is widely used in injection molding. It is an affordable and versatile material that is strong and rigid. ABS is also non-toxic, making it a good choice for products that will be used in contact with food. Additionally, ABS is easy to machine and can be injection molded into a variety of shapes and sizes. This makes it a good choice for products that need to be mass-produced.
(PC) Polycarbonate Injection molding material
Polycarbonate is a very versatile engineering plastic that is used in a wide range of applications. It is tough, transparent and shatter-resistant, making it a great material for safety products like eyeglasses and helmets. Polycarbonate parts can also be very thin and lightweight, making it a popular choice for medical devices and consumer electronics. Thin-walled parts can also be molded, making it an ideal choice for tight-tolerance parts with complex geometries.
( Aliphatic Polyamides) PPA Injection molding material
Aliphatic polyamides, or PPAs, are a family of thermoplastic polymers. They have excellent resistance to chemical and environmental degradation, making them a perfect choice for applications that require toughness and durability. PPAs are also resistant to abrasion and wear, making them a good choice for products that see a lot of use. Some of the most common applications for PPAs include automotive parts, sporting goods, medical devices, and construction equipment.
(Polyoxymethylene) POM Injection molding material
Polyoxymethylene (POM, also known as acetal) is a thermoset plastic with a high resistance to wear and fatigue. It is also inert to most chemicals and resistant to staining. This material is commonly used in the production of high precision parts for the automotive and engineering industries.
(Polymethyl Methacrylate) PMMA Injection molding material
Polymethyl Methacrylate (PMMA) is a versatile thermoplastic with good transparency and weather resistance. It is often used as a molding material because it can be easily colored and shaped. PMMA is also resistant to chemicals and can withstand high temperatures, making it a good option for products that need to be durable.
4. What are the benefits of plastic injection molding?
Plastic injection molding is a manufacturing process that uses a heated barrel to force molten plastic into a mold. The mold is then cooled and opened to release the finished product. This process can be used to create products in a variety of shapes and sizes, and it offers several benefits over other manufacturing processes. Perhaps the biggest benefit is the ability to create products in large quantities. This makes plastic injection molding a cost-effective option for businesses that need to produce large quantities of products. The process is also reliable and can produce high-quality products.
5. Industries that rely on plastic injection molding
Here are the four main industries that rely on plastic injection molding:
#1 Health and Beauty Startups
Health and beauty startups are a dime a dozen. In fact, it seems like a new one pops up every other day. So, what makes one stand out from the rest? Quality products, attention to detail and an innovative approach are a few things. But, let’s not forget about the importance of presentation. If your product isn’t packaged well, it will likely end up in the trash. That’s where plastic injection molding comes in. This manufacturing process allows startups to produce high-quality, affordable and innovative packaging for their products. From shampoo bottles to contact lens cases, plastic injection molding is relied on by health and beauty startups to get their products off the ground.
#2 Food Packaging Innovators
Plastic injection molding is used in a variety of industries, from aerospace to automotive. One industry that has been tremendously impacted by this manufacturing process is food packaging. In the early days of injection molding, food companies were some of the earliest adopters of the technology. They quickly realized the benefits of using molded plastic containers to package their products. Molded plastic is a great material for food packaging because it is durable, lightweight and food-safe. Food packaging innovators have continued to rely on plastic injection molding over the years to create new and innovative products.
#3 Medical Device Innovators
One of the key benefits of plastic injection molding is its ability to create intricate and complex designs. This is especially beneficial in the medical device industry, where innovators are always coming up with new and ingenious ways to improve patient care. From syringes and sutures to tiny sensors and surgical tools, plastic injection molding is a vital part of bringing new medical devices to market. In fact, it’s hard to imagine a world without some of the life-saving devices that have been made possible by this manufacturing process.
#4 Auto Industry Contributions
Plastic injection molding is used all over the world in a variety of industries. It’s a process that helps to create products that are both durable and efficient. In the auto industry, for example, plastic injection molding is used to create everything from dashboard components to fuel tanks. The process is quick and relatively easy, which is why it’s become a popular choice for manufacturers. It’s also a cost-effective option, which is why so many companies rely on it.
6. How Effective is Plastic Injection Molding?
The short answer is very effective. Plastic injection molding is widely considered the most efficient and effective manufacturing process for producing high-quality products. Not only does it allow for a high degree of control over the product’s final form and function, it also delivers a high degree of consistency from one product to the next. This is because the injection molding process is highly automated and tightly controlled, which results in a very high degree of repeatability. As a result, plastic injection molding is the process of choice for many industries, including automotive, medical, and consumer goods.
Categories
Share On
Recent Post
CNC Machining Design Guide
CNC machining—short for computer numerical control machining—turns a digital CAD model into
CNC Machining Guide Explained
Computer Numerical Control (CNC machining) is a cornerstone of modern