Injection molding factory will give you the answer to this question through an article that discusses how long injection molds last and some tips to make sure they do last long enough to turn your product idea into a successful business. To get the most out of your injection molding machine, you need to understand it better and adjust its use based on the type of material you’re working with. You’ll also have to take steps to ensure its longevity since in many cases, an injection mold might be the only tool standing between your business and bankruptcy if it breaks down too soon.
Environment factors
Temperature is a key environmental factor in determining injection-molding durability. In general, thicker sections and walls are more durable than thinner ones because they require less cooling time. The standard maximum thickness for injection-molded parts is 4 mm; most molds have to be rebuilt when working at or near that limit. But some molds can produce castings up to 8 mm in thickness before needing a rebuild. That’s because such molds can build up higher internal pressures before breaking due to their greater cooling capacity. For example, they may use insulation blankets around sections that would otherwise need thick supports or other extra strengthening features inside the mold cavity to prevent warping under pressure.
Quality factors
There are many factors that influence quality when it comes to injection molded products. The thickness of an injection mold and type of plastic play a major role in determining durability. While thicker molds allow for more consistency in product size and shape, they can only be used with certain plastics. Thinner molds can be used for a wide range of plastics but do not hold up as well to Injection pressure and temperature changes. This leads to more defects and lower overall quality. Once you have decided on a standard for your product design, consult with your injection molding factory about thickness options so you know what size molds are best suited for your project.
Mold design
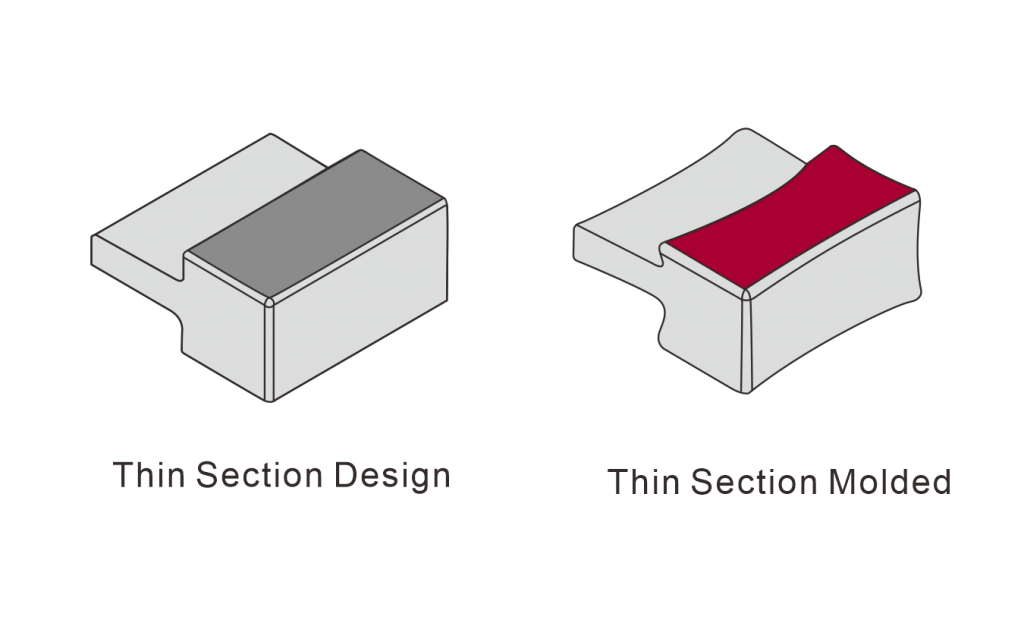
Thickness of injection mold is largely related to its size and complexity. Because larger molds have more internal cavities (particularly for highly detailed parts), they will weigh more and may have trouble fitting in standard injection machines. So what’s it all mean for you as a customer? It could require higher design costs or higher part costs to make your product a reality with these kinds of molds. The injection molding factory will also be more selective about which customers it takes on—especially those with complex designs—because they will understand that there are many potential pitfalls in manufacturing such smaller-scale molds. To make things even trickier, having thinner walls makes it harder to fill them with material, which leads to defects when building larger parts.
Mold maintenance
Every injection mold is different. Take care and maintain it according to its needs. There are a variety of things you can do to take care of your injection molds such as: proper storage after use; periodic maintenance cleaning; mechanical lubrication; regular maintenance inspection; timely replacement if broken parts. Under normal circumstances, if you treat your molds well and pay attention to them during work, it could still be used for years or even decades before failure.
Injection molds
What’s it really like to work in an injection molding factory? Injection molds are used to create plastic parts by forcing molten plastic into them. This creates a negative impression (like a vulcanized shoe sole) which is filled with liquid polymer. Afterward, it’s heated to give it its final shape. A typical injection-molding cycle takes 10 seconds; however, if you take into account cooling time (about 60 seconds), cycle time is only about seven seconds. They usually have a minimum shot size of 250 grams and can range anywhere from 500 grams to 20 kilograms or more depending on what they’re being used for.
Length of Cycles
The length of a cycle depends on many factors. The shorter it is, the less time parts spend in or near hot zones and therefore less heat exposure. A longer cycle will obviously have more total time at higher temperatures; but if part exposure is limited to a short amount of time that doesn’t matter as much. As with most things in injection molding, there are other tradeoffs; when you run your cycles faster you also tend to increase cycle pressures which can lead to non-uniform shrinkage and off-shooting/breakage. Faster isn’t always better. At least, not for all molds.
Injection Molding Wall Thickness Constraints
The wall thickness of an injection molded part is a key factor in determining both part strength and manufacturability. While thin walls are desirable for minimal weight or aesthetic design aspects, thin walls also typically require more processing time and reduce material yield. Therefore, it is important to achieve a balance between thin-wall aesthetics and practical manufacturing costs. Factors such as material choice, resin density and fill distribution can be used to minimize wall thickness while keeping production costs at a minimum. All these factors should be considered when designing or selecting components for your product’s assembly process. Knowing that your parts can have an acceptable range of wall thickness will assist you in making informed decisions on manufacturing processes as well as overall cost optimization throughout your product development cycle.
Solutions for Thick Walls
Wall thickness is one factor in terms of material selection. You’ll also want to consider a variety of other factors such as your part’s tolerance for warpage, its pressure and temperature requirements, desired cycle time and your mold design process. Although there are no set standards for wall thickness in injection molds (or any industry standard), it’s safe to say that thicker walls usually take longer to cool and will require more clamping force during ejection. The basic rule here is that thinner walls make better parts. But what if you absolutely need thicker walls?
Sharp Corners
Rounder corners in a product may have a negative impact on durability. It is well known that sharp edges and corners reduce product durability as stress concentration develops at these locations during use. They are also susceptible to fracture in field conditions especially when subjected to external stress or impact. To test for corner sharpness, press your fingernail into one corner of a plastic part, if it goes in easily more than 1mm then it should be filed back until your fingernail just skims over it. If you file too much material from an edge or corner you must re-evaluate design and ensure that material has not been removed unnecessarily.
Categories
Share On
Recent Post
Symmetry (GD&T) Guide
Have you ever looked at a complex part and wondered
What is Angularity (GD&T)?
Have you ever looked at a technical drawing and seen